Recognizing the Fundamentals and Applications of Plastic Extrusion in Modern Manufacturing
In the world of contemporary production, the method of plastic extrusion plays a critical function - plastic extrusion. This elaborate process, including the melting and shaping of plastic with specialized passes away, is leveraged across numerous markets for the development of varied items. From vehicle components to consumer products packaging, the applications are large, and the potential for sustainability is equally outstanding. Deciphering the basics of this procedure reveals real flexibility and capacity of plastic extrusion.
The Principles of Plastic Extrusion Refine
While it may appear complex, the fundamentals of the plastic extrusion procedure are based on relatively straightforward concepts. It is a production process wherein plastic is thawed and after that formed into a continual account through a die. The plastic extrusion procedure is extensively made use of in different industries due to its versatility, performance, and cost-effectiveness.
Different Types of Plastic Extrusion Strategies
Building upon the fundamental understanding of the plastic extrusion procedure, it is necessary to explore the numerous strategies entailed in this production technique. In contrast, sheet extrusion creates large, level sheets of plastic, which are generally further processed into items such as food product packaging, shower drapes, and vehicle parts. Recognizing these techniques is key to using plastic extrusion effectively in modern-day production.
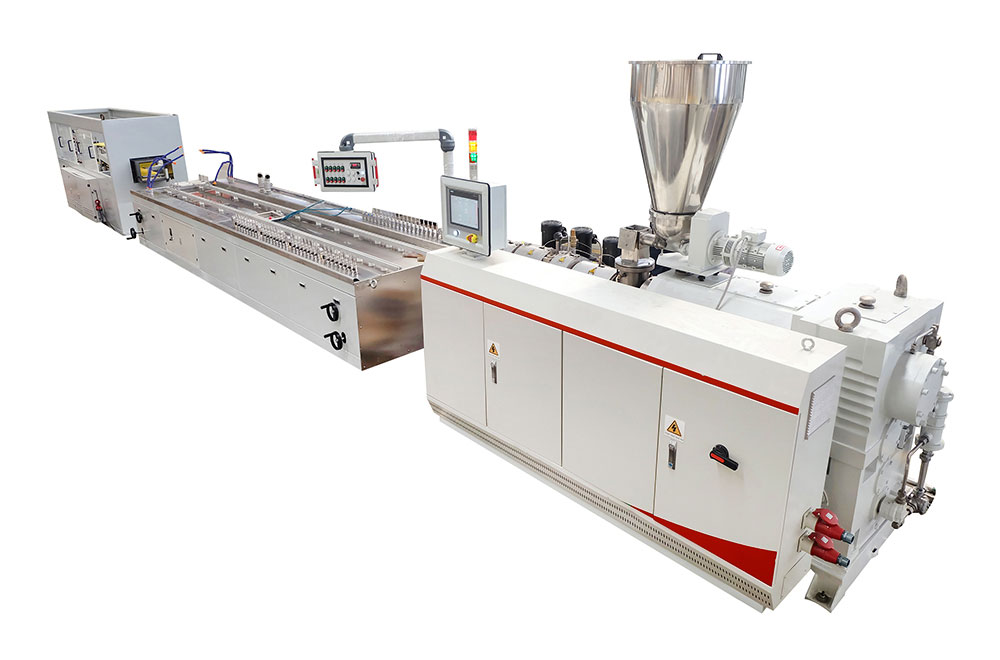
The Role of Plastic Extrusion in the Automotive Sector
A frustrating bulk of components in modern-day automobiles are items of the plastic extrusion process. Plastic extrusion is largely utilized in the manufacturing of numerous automobile components such as bumpers, grills, door panels, and dashboard trim. Hence, plastic extrusion plays a pivotal function in vehicle production.

Applications of Plastic Extrusion in Durable Goods Manufacturing
Beyond its substantial impact on the vehicle sector, plastic extrusion confirms equally efficient in the world of customer items manufacturing. The adaptability of plastic extrusion permits producers to make and produce complex shapes and sizes with high accuracy and efficiency. The flexibility, versatility, and cost-effectiveness of plastic extrusion make it a recommended choice for many consumer products suppliers, adding significantly to the market's growth and technology.
Environmental Impact and Sustainability in Plastic Extrusion
The pervasive usage of plastic extrusion in making invites analysis of its environmental implications. Reliable equipment see this decreases energy use, while waste management systems recycle scrap plastic, reducing raw product demands. Regardless of these improvements, better technology is needed to alleviate the environmental impact of plastic extrusion.
Final thought
To conclude, plastic extrusion plays an essential function in modern production, specifically in the vehicle and durable goods markets. Its flexibility permits for the production of a variety of parts with high precision. Its capacity for recycling have a peek at this website and growth of eco-friendly materials uses an encouraging avenue towards sustainable techniques, thereby dealing with ecological concerns. Recognizing the basics of helpful resources this process is essential to optimizing its applications and advantages.

The plastic extrusion process is thoroughly utilized in different industries due to its cost-effectiveness, performance, and convenience.
Building upon the basic understanding of the plastic extrusion procedure, it is needed to discover the numerous methods entailed in this manufacturing method. plastic extrusion. In comparison, sheet extrusion creates huge, flat sheets of plastic, which are normally additional refined into items such as food packaging, shower drapes, and auto parts.A frustrating bulk of components in modern-day vehicles are items of the plastic extrusion process